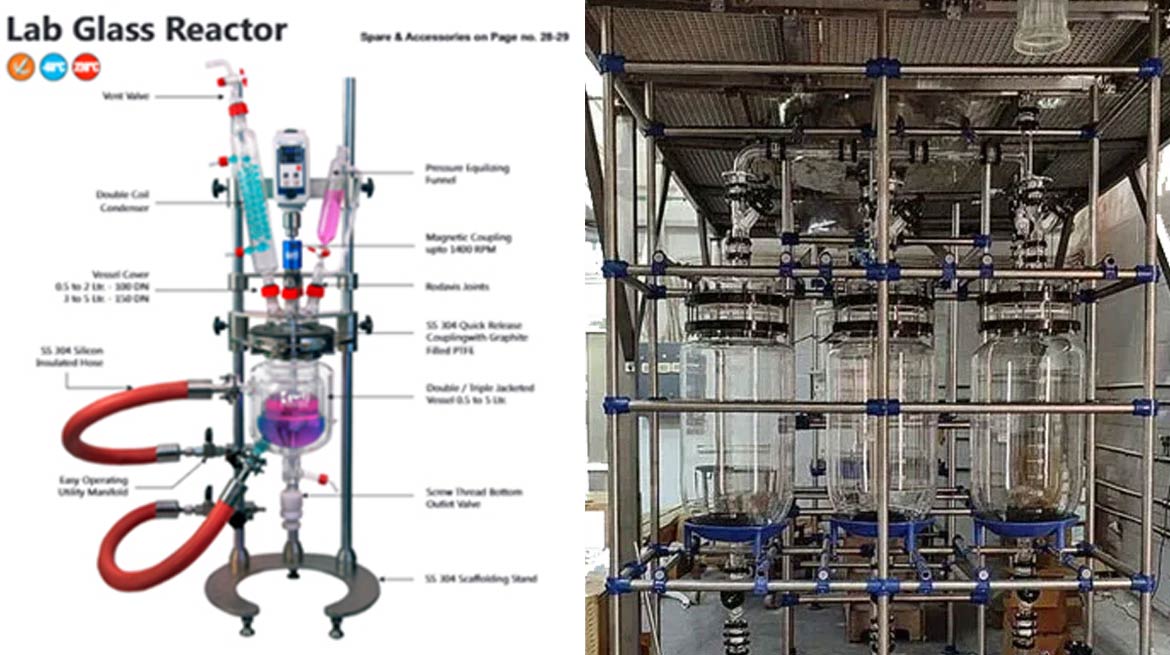
Best Laboratory Glass Reactor Manufacturers & Suppliers by Goel Scientific Glass Inc. USA & CANADA: 1 Ultimate Guide
-
Viral Limbachiya (Digital Marketing)
-
March 28, 2023
-
-
1 Comment
Lab Glass Reactor
Lab glass reactors are incredibly efficient devices when it comes to mixing, dispersing,homogenizing, and optimizing chemical reactions on a laboratory scale. They featurecorrosion-resistant qualities, a clear view of the reaction process, and good performance in vacuum and atmospheric pressures. These reactors are popular for many applications because they increase productivity, precision, and total repeatability.
Best Laboratory Glass Reactor Manufacturers & Suppliers
Lab glass reactors are premium, fire-resistant reactors that provide the best possible process performance in lab settings. They are connected to auxiliary devices such as Nox Gas Scrubbers, Distillation unites, and Agitated Nutsche Filters. Processing of acids and Solvents Recovery in a sealed reaction tank is made safe by the fireproof design. Goel Scientific Glass has experience building reactors to meet customer specifications and provides a large selection of vessel alternatives. Certainly, their highly qualified experts put in endless effort to design and produce glass reactors in accordance with requirements. In most glass plants, vessels are used as reactors, receivers, separators, and measuring or feed vessels.
1. What is a Lab Glass Reactor?
Glass reactors are utilized in the chemical and pharmaceutical industries because they are compatible with a wide variety of substances. An agitator is built within the reactor, a container that allows chemicals to mix in a controlled setting.
The reactor may function in a variety of temperatures and under pressure. The reactor's upper part facilitates the connection of the process nozzles, which introduce chemicals and gases as needed and enable cleaning head nozzles. They come in a variety of sizes, but the standard range is 5 Ltr to 100 Ltr. Glass Reactor is available in Spherical Shape from 5 to 500 Ltr and in Cylindrical Shape from 5 to 500-Ltr capacity. Cylindrical vessels can be supplied with metal/glass jackets too. In most glass plants, vessels are used as reactors, receivers, separators, and measuring or feed vessels.
2. Types of Lab Glass Reactors
- Stirrer with suitable mechanical seal/stuffing box/magnetic seal.
- Volume of Lab Glass Reactor: 500 mL to 5000 ml.
- There are three types of reactors: single, double, and triple walls.
- Operating Pressure: 0.5 bar (g) to full vacuum
- -50°C to +180°C is the operating temperature range.
- Thermal shock resistance (Dt): triple-walled reactors at 60°C and double-walled reactors at 11
3. High pressure Glass Reactor
A High – pressure Glass Reactor is a specialized vessel designed for chemical reaction elevated pressure, achieved by the reaction itself or externally supplied source like hydrogen. Operating at temperatures above solvent boiling points, these reactors impact reaction dynamics by increasing concentration $ collision frequency among molecules, accelerating reactions.
Widely used in industries requiring precise control over reaction, such as organic synthesis & pharmaceutical development. There control environment facilities effects efficient exploration & optimizatation of various chemical reaction .
4. How Lab Glass Reactors Work
Reactors function by letting chemicals into a confined area and stirring them using an agitator in the middle. Baffles are usually incorporated into the vessel to guarantee enough internal turbulence to mix and blend the chemicals and activate the reactor. Normal chemical reactions occur when the right catalysts, chemicals, pressure, temperature, and contact time are present. Furthermore, the final result could be liquid or solid.
5. Applications and Industries
Glass reactors are useful in the biotechnology, Chemical, & pharmaceutical R & D. They can be used for many different things, such as:
- Chemical synthesis: The chemical and pharmaceutical industries employ glass reactors to synthesize a variety of compounds.
- Polymerization: Resins, adhesives, and plastics are among the materials that may be polymerized in glass reactors.
- Distillation: Valuable compounds are recovered, and solvents are distilled using glass reactors via fractional distillation.
- Crystallization: Chemical compounds can crystallize in glass reactors.
- Extraction: Plant materials are extracted, natural products are isolated, and compounds are purified using glass reactors Via steam & Vacuum Distillation method
- Wiping Film Evaporator: Sensitive products like Vitamins, Hormones enzymes, or aromatic substance reaction under vacuum forming thin film to reduced time using glass Column / reactor
FAQs:
1. Are there different types of lab glass reactors, and how do I choose the right one for my needs?
Think about the following while selecting your next-line reactor:
- Class of insulation
- A minimum heat increase of 115°C is to be expected.
- Request the development of a vacuum pressure impregnation system.
2. What safety precautions should I take when working with lab glass reactors?
Always wear the proper safety gear, such as gloves, a face shield, and safety goggles. When feasible, use glassware with a PVC coating. Cover flasks, drawers, and desiccators with mesh or tape if not available.
3. How do I clean and maintain a lab glass reactor?
More satisfying results will come from using a cleaning powder with a little abrasive effect on very unclean glassware. Certainly, a brush can thoroughly clean every portion of the glassware throughout the washing process.
4. What size options are available for Lab Glass Reactors?
Goel Scientific Glass supplies Bench top Lab Glass Reactors. This contains 5000L to 50L containers with Single, Double & Triple walls.
5. Can I customize a glass reactor to meet my needs or add additional features?
Yes. Lab Reactors are built from a variety of materials according to your needs. All you have to do is search for the Custom laboratory glassware manufacturer near me, and Goel Scientific will be available at your service.
Need top-notch laboratory glassware manufacturers? Goel Scientific Glass a reliable and renowned name when it comes to top-grade lab equipment, including laboratory glass reactors. Contact us today for a quote.
Salient Features
- Glass Reactors made from Germany Raw Material.
- Lab Reactor system suitable for most bench top fume hoods.
- Stirrer with suitable mechanical seal/stuffing box/magnetic seal.
- Skid Mounted and quick release clamp for easy installation & removable of glassware.
- Suitable for vacuum condition
- Flush bottom with minimum dead volume.
- Overhead Stirrer geared motor with built-in speed controller & display.
- Measurement Marking on the vessel.
- Interchangeable Stirrer anchor, propeller, turbine Digital temperature indicator
Reactors equipped with the flush bottom valve of the special type to ensure leak-free sealing over entire temperature rang.
All These Reactors are designed GMP.
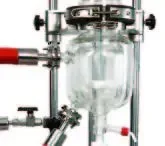
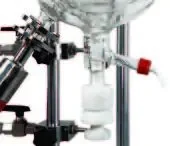
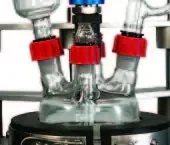
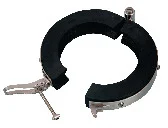

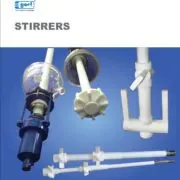
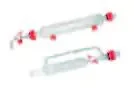

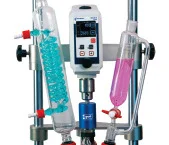
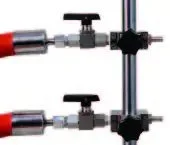
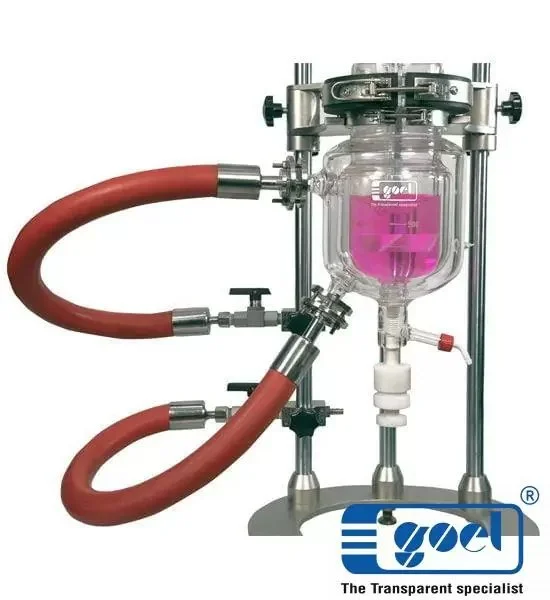