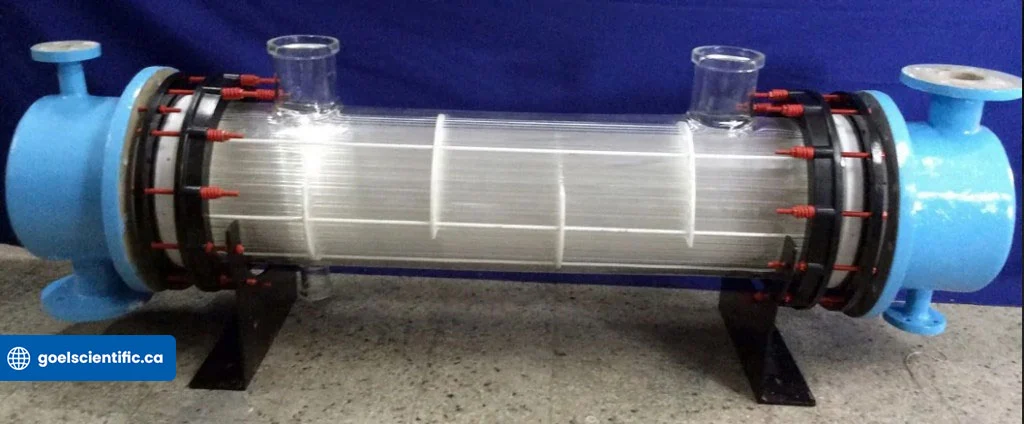
Shell and Tube Glass Heat Exchanger by Goel Scientific Glass Inc. USA & CANADA: 1 Ultimate Guide
-
Viral Limbachiya (Digital Marketing)
-
June 11, 2023
-
-
1 Comment
Shell and Tube Glass Heat Exchanger
The versatility of shell and tube heat exchangers in managing a broad spectrum of temperatures and pressures makes them widely used. They fall into two primary categories: those used in the power business, such as feed water warmers and power plant condensers, and those used in the petrochemical industry, governed by TEMA regulations. Every industry has similar features to the exchanger.
Borosilicate Glass Heat Exchangers
The overall heat transfer co-efficient of Borosilicate glass Heat Exchanger equipment is comparatively favourable with many alternative materials because of its smooth surface which improves the thermal coefficient & reduce the tendency of fouling
Heat Exchangers are available in 2 basics designs:
- Conventional Coil Type Condensers heat exchangers.
- Shell & Tube Type Glass heat exchangers
Shell &Tube Heat Glass Exchanger Manufacturers The USA
One of the leading shell and tube glass heat exchangers manufacturers in the USA, Goel Scientific Inc. provides a variety of shell and tube heat exchangers used for a variety of applications, such as heating or cooling process fluids, preheating or cooling air before it enters an industrial furnace, or condensing steam. Depending on the application, they can be designed with multiple passes to increase efficiency or with special features such as removable bundles to facilitate cleaning Available in a range of sizes and materials, our heat exchangers are used across a variety of industries including pharmaceutical, chemical, food & beverage and oil & gas These heat exchangers transmit heat between substances efficiently and economically, saving energy. The bundle of hollow tubes that serve as a single fluid's flow channels are housed inside the pressure vessel or shell.
Although the tubes are composed of materials that transport heat, they need to be strong enough to endure structural stress during heat exchange. For these heat exchangers, metals, including titanium, nickel, steel, and copper alloy are excellent options.
These heat exchangers are an affordable option for a number of uses as they can accept waste heat from industrial production operations. Shell and tube heat exchangers are great for effective and economical heat exchange.
Goel Scientific, is pioneers in the field & a leading in Glass shell and tube heat exchanger Coil type Glass heat exchanger & product has a wide acceptability for more information search with keywords “Industrial Glass ware” to get contact details.
1. What is a Glass Shell and Tube Heat Exchanger?
Shell-and-tube heat exchangers are a kind of heat exchanger. It is suitable for application where large heat transfer are required in limited space most prevalent heat exchange in Pharmaceutical and other sizable chemical operations. Main object of Glass shell & tube heat exchanger are condensation & Evaporation in large surface area.
2. Types of Shell and Tube Heat Exchangers
There are many different types of glass heat exchangers available on the market today. Some common types include plate and shell heat exchangers, tube and shell heat exchangers, and double pipe heat exchangers. Each type has its own advantages and disadvantages that should be considered when selecting a heat exchanger for a particular application.U-tube, floating head, and fixed tube heat exchangers are the three primary shell and tube heat exchanger varieties.
3. Advantages of Glass Shell and Tube Heat Exchanger
Some of the advantages are as follows:
- It is less expensive than heat exchangers using glass tubes
- Corrosion resistance an alternative like graphite hostelry, copper, titanium & other exotic metals
- It is very easy to replacement of tubes cleaning with a straight forward design.
- The delta P/ΔP pressure drop is lower than that of a plate heat exchanger.
- Simple to locate and separate leaky tubes
4. Advantage over Glass Coil type Heat Exchanger
Some of advantages are as follows:
- The overall heat transfer coefficient in Glass shell & tube heat exchanger is about 3 times higher in coil type heat exchanger
- The pressure drop in shell & tube heat exchanger is minimum compared to coil type glass heat exchanger
- For requirement of higher heat transfer area shell & tube heat exchanger is only alternative.
5. Salient Features of Glass Shell and Tube Heat Exchanger.
Simple in design, sturdy in nature, and somewhat inexpensive to buy and maintain are the features of shell and tube heat exchangers. Even while they take up more room than a plate heat exchanger with a comparable thermal exchange capacity, they also have a very high heat transfer rate.
6. Construction Features of Shell and Tube Heat Exchanger
It is a device with several tubes inside a cylindrical shell that go via tube sheets and baffles. When heating, one fixed sheet permits thermal expansion. ' Shell side' refers to the flowing medium outside the tubes, and 'tube side' refers to the flowing media inside the tubes.
The glass tubes are sealed individually into PTFE tube sheet with PTFE sockets & packing PTFE Baffles on shell side ensure improved heat transfer by increased turbulence
Made from borosilicate Tubes SCHOOT DURAN. Joint less tubes offer better pressure rating
The glass tubes are sealed individually into PTFE tube sheet with PTFE sockets & packing PTFE Baffles on shell side ensure improved heat transfer by increased turbulence
Made from borosilicate Tubes SCHOOT DURAN. Joint less tubes offer better pressure rating
Since each tube may function as a tiny pressure vessel, the tube side medium is usually utilized for high-pressure fluids. Producing high-pressure-rated tubes is more economical than producing high- pressure-rated shells. As an example, a shell heat exchanger employs water as the tube side medium and oil as the shell side medium to cool the oil. The top left entrance of the heat exchanger is where the oil enters, and it travels down the tubes to the lower right discharge.
7. Choosing the Right Glass Shell and Tube Heat Exchanger for Your Needs
Your decision about the kind of heat exchanger is influenced by a number of variables, including the fluids' pressure, temperature, and corrosiveness; the necessary heat transfer area and efficiency; the space and accessibility for maintenance; and the upfront and ongoing expenditures.
8. Why Choose Us?
Choosing the best heat exchanger design for transferring heat between fluids might be challenging. Goel Scientific Inc. can help you whether you need new units for new processes, direct replacements for worn-out or inefficient heat exchangers, or components to keep your present units working. Contact us to find out how we can assist!
You can also perform a quick web search with the keywords ‘Industrial Glassware Manufacturer near me’ to get out contact details.
FAQs:
1. How does a Shell and Tube Heat Exchanger Work?
The shell and tube sides are the two primary systems of a shell and tube heat exchanger. Cooling water is included on the tube side, and hot mineral oil or Vapour is on the shell side. Cooling water enters the heat exchanger and travels through the tubes while the mineral oil enters and circulates in the shell around the tubes.
This indirect cooling is because the turbulent flow created by the fluids' non-direct mixing speeds up heat transfer and lessens the possibility of dissolved particles building up on the walls of the tube and shell. Baffles generate turbulent flow within the shell, whereas tube inserts create turbulent flow within the tubes. The two fluids exchange heat, with the water exiting the heat exchanger warmer and the oil leaving it colder.
2. How do you calculate the area of the Shell and Tube Heat Exchanger?
To figure out how big a shell and tube heat exchanger is:
- Determine the fluids on the shell and tube sides.
- Find the coefficients of heat transfer.
- Determine the heat transfer coefficient overall (U).
- Calculate the temperature difference (ΔT).
- Log mean temperature difference (LMTD) should be calculated.
- Use Q = U * A * LMTD to find the necessary area.
- Think about the practical aspects of layout and size.
3. How to Clean the Shell and Tube Heat Exchanger?
Hydro chemical and alkaline water circulation cleaning glass tube inside & outside are the three most used techniques.
4. How to Design a Shell and Tube Heat Exchanger?
By specifying criteria for materials, design, manufacturing, and inspection, code regulations and standards seek to assure safe construction and public protection. The API (American Petroleum Institute), ASME (American Society of Mechanical Engineers), TEMA (1998), HEI (1980), and other mechanical design standards and pressure design codes are utilized in the construction of heat exchangers. One must consider these rules for designing a Shell and Tube Heat Exchanger. The operating dangers might arise if these rules are disregarded.
5. What are Shell and Tube Heat Exchangers Used for?
The food, chemical, oil and gas, and other industries like pharmaceutical & chemical all employ Glass shell and tube heat exchangers. They serve as condensers and evaporators.
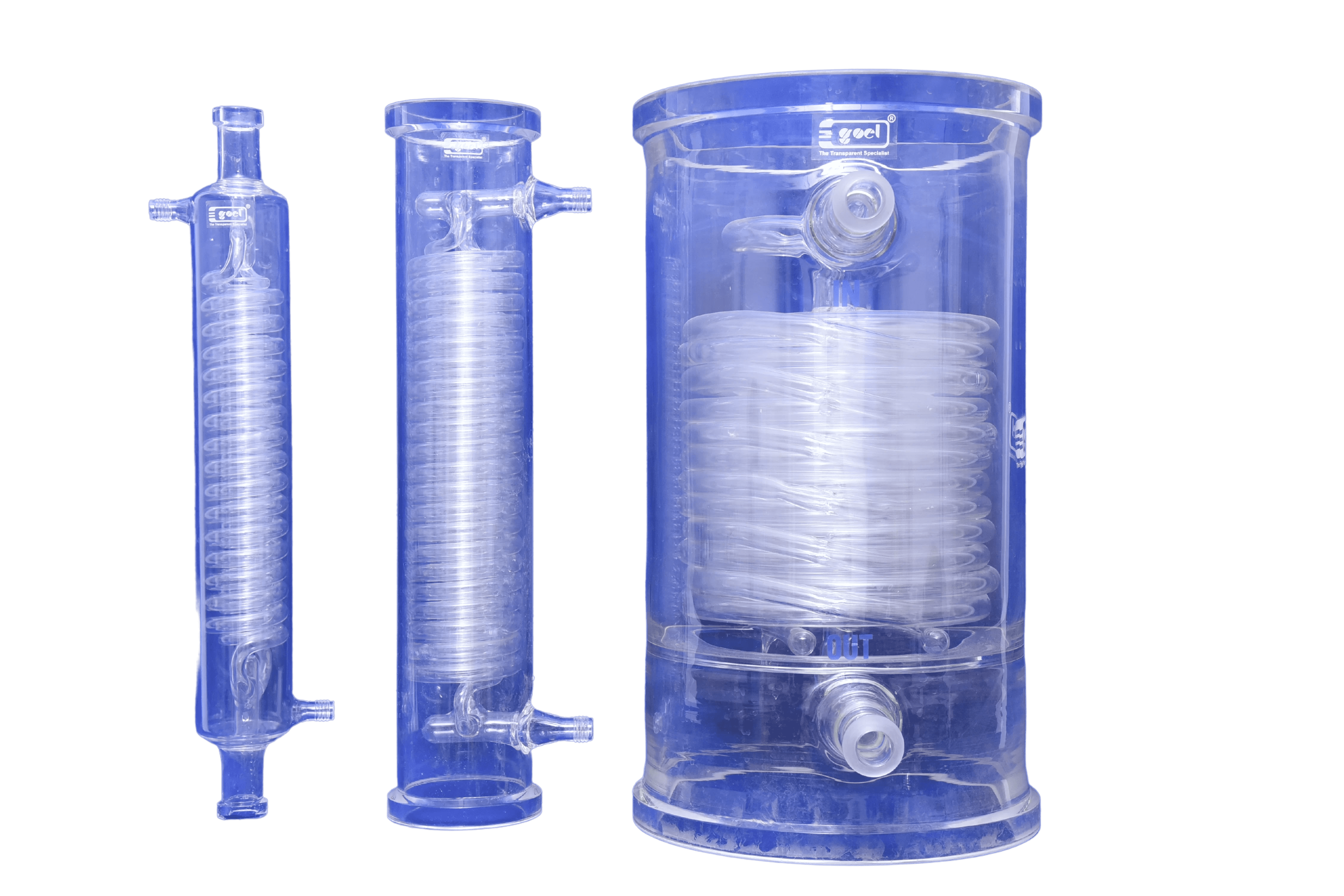
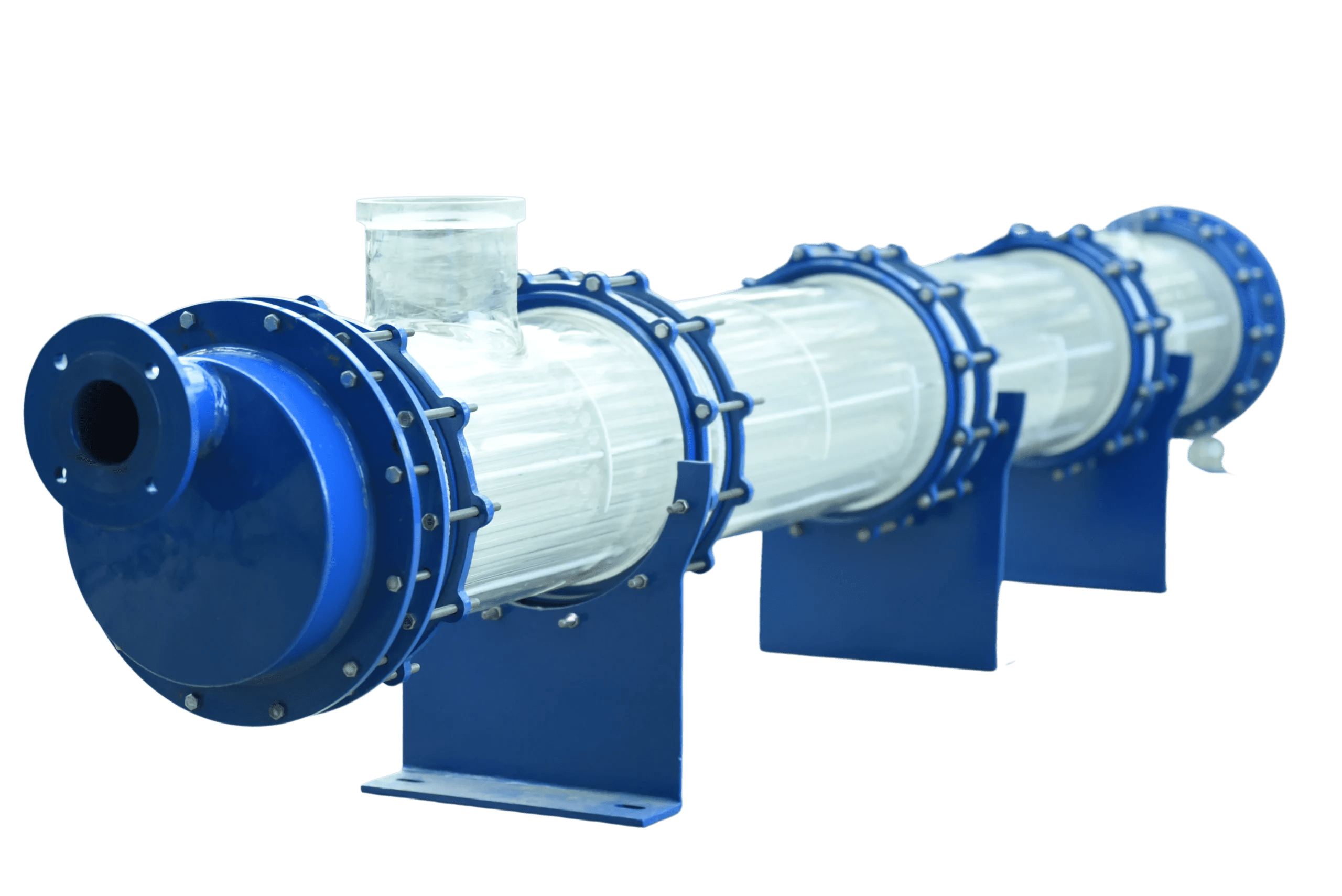
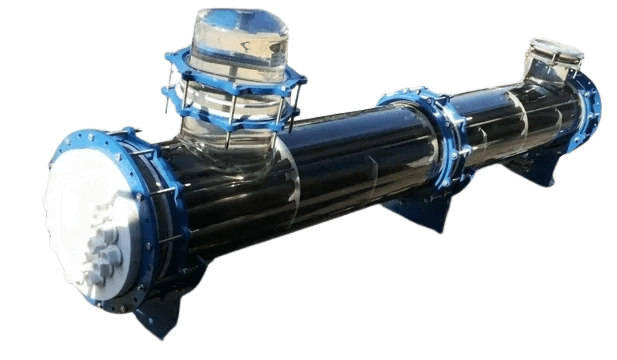