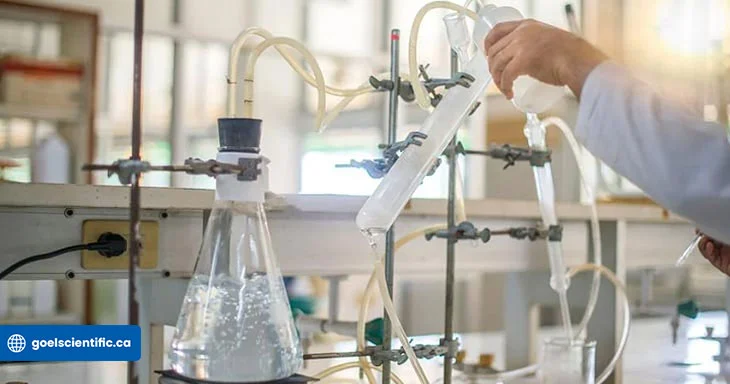
Best Fractional Distillation Unit by Goel Scientific Glass Inc. USA & CANADA: 1 Ultimate Guide
-
Piyush Shah (Business Director)
-
August 5, 2023
-
What is Fractional Distillation?
Fractional distillation is the separation of various components from a liquid homogeneous mixture. Each component typically has a different boiling point and vapour pressure than the rest, so fractional distillation can be achieved by applying a temperature gradient.
The various components are condensed at different stages or levels of the setup, which can either be a small setup consisting of laboratory glassware and other equipment, or a large-scale industrial operation, such as in the oil and gas industry when refining petroleum into different types of fuel.
Fractional distillation is typically used when there are more than two components in a liquid mixture that need to be separated. The differences in the boiling points of the liquids make it possible to condense the liquids at various points of the fractionating column.
Both small-scale and large-scale laboratory fractionating columns have the same basic designs: The various types of vapours are condensed and collected at various levels corresponding to their volatilities.
What is the Purpose of Fractional Distillation?
Fractional distillation is very useful when separating more than two types of liquids from a homogeneous mixture. This method is particularly useful in separating liquids that have less than 25°C difference in boiling points. It can also be used to increase the purity of a particular distillate. During fractional distillation, fractions of the original mixture are evaporated and condensed at different levels as the temperature gradient changes.
Although an ordinary distillation method can also be used to separate mixtures consisting of more than two types of liquids, it would be tedious, time consuming, and impractical to redistill the same liquid mixture repeatedly at different temperatures just to separate the different components.
The elegant solution to this problem is using temperature gradients. This can be done either by using a fractionating column or separate distillation chambers in sequence. Here’s how the sequential distillations process works:
What Are the Different Types of Distillation?
There are several different types of distillation, owing to its range of industrial applications. The exact step-by-step process and equipment details of each type are beyond the scope of this article, but we’ll outline the generalised process and concepts of each one.
Fractional Distillation
This is essentially a compact batch-type fractional distillation unit in which the reboiler consists of a vessel mounted in a heating bath and with a packed column above. The vapours from top is condensed and can be refluxed as per requirement.
The top product is sub-cooled and collected in receivers. The bottom product is finally drained from the reboiler through a drain valve.
The units are available in vessel sizes of 20, 50, 100, 200, 300 & 500 L and is suitable for operation under atmospheric pressure and full vacuum.
UNIT CAT. REF. | REACTOR CAPACITY | BATH KW | VAPOUR LINE | CONDERSER HTA M2 | COOLER HTA M2 | RECEIVER SIZE |
---|---|---|---|---|---|---|
FDU20 | 20 L | 4.0 | 80 DN | 0.35 | 0.10 | 2L , 5L |
FDU50 | 50 L | 6.0 | 100 DN | 0.50 | 0.20 | 5L , 10L |
FDU100 | 100 L | 9.0 | 150 DN | 1.50 | 0.35 | 10L , 20L |
FDU200 | 200 L | 12.0 | 150 DN | 1.50 | 0.35 | 20L , 20L |
FDU300 | 300 L | 18.0 | 225 DN | 2.50 | 0.50 | 20L , 20L |
FDU500 | 500 L | 24.0 | 300 DN | 4.00 | 0.70 | 20L , 50L |